The “Medium Combustion Plants Directive” (MCPD) and its impact on process heat plants
Article written by
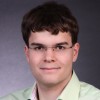
Achim Schwarz
Does your company operate process heat plants in the EU with a rated thermal input of up to 50 MW? Then you are advised to read this article, because nothing less than the continued legal operation of your plant is at stake!
The EU’s “Medium Combustion Plants Directive” (MCPD) came into force at the end of 2018 and sets minimum standards for exhaust emissions from combustion plants between 1 and 50 MW, both for new and existing plants.
It was transposed into national law by the individual member states, whereby the limits are often even stricter, especially in Western Europe (e.g. lower NOx limits or earlier entry into force for existing plants).
Due to special rules of the national regulations, even plants < 1 MW can be affected in some cases (e.g. in Germany for plants requiring a permit)! In this article, I will focus on existing plants that are fired with gaseous (mostly natural gas) or liquid (mostly fuel oil) fuels, because in my experience, especially smaller plant operators are often not yet sensitised to the issue in these cases.
I consider plants with burners, i.e. I disregard engine and gas turbine plants.
I also focus on nitrogen oxides (NOx), as these are often the sticking point. Emissions of carbon monoxide (CO), sulphur dioxide (SO2) or dust particles (PM) are usually irrelevant for these plants or at least much less critical.
What are the NOx limit values (EU minimum requirement!) for existing plants and when do they come into force?
Limit values in mg/Nm³, based on 3% oxygen content in the flue gas:
- Natural gas and other gaseous (e.g. liquefied petroleum gas – LPG): 250 (but 200 for natural gas > 5 MW!)
- Fuel oil: 200
Entry into force:
- From 01.01.2025 for plants > 5 MW
- From 01.01.2030 for systems up to 5 MW
How can national tightening or complexities (partly also illogical and rationally hardly comprehensible) look like?
This will be demonstrated here using the example of Germany, where the “44th Federal Immission Control Ordinance” (44. BImSchV) sets the corresponding limit values:
- In nearly all cases, even plants up to 5 MW are affected as early as 01.01.2025! (Until the end of 2024, the previous limit values as stipulated in the TA Luft – for installations requiring a permit – and in the Ordinance on Small and Medium-Sized Combustion Plants – for installations not requiring a permit – will apply to all existing installations).
- With regard to the limit values, a distinction is generally made between two cases:
- Installations not requiring a permit < 10 MW
- Installations from 10 MW and all installations requiring a permit.
- In case 1, the NOx limit value for natural gas and LPG for existing plants is initially 150 mg/Nm³, but only temporarily until the end of 2035. From 2036 onwards, the limit value drops 100 mg/Nm³, as for new plants! [In Germany, liquefied petroleum gas is treated just as strictly as natural gas, although higher emissions are hardly avoidable with identical technology].
- In case 2, stricter regulations also apply. For example, the NOx limit value for natural gas or LPG for typical thermal oil heaters (> 210 °C) or steam/hot water boilers for higher pressures (> 18barg) is also 150 mg/Nm³. At lower temperatures or pressures (110 to 210 °C or 0.5 to 18 barg) it drops to 110 mg/Nm³, then a tightening to 170 mg/Nm³ also applies to fuel oil. [A temporary limit regulation and then subsequent tightening is not included in case 2 (for the time being?)].
What exemptions can apply?
First of all, the MCPD and, in most cases, the respective national implementations do not apply to certain types of installations, e.g. directly flue-gas heated dryers.
Furthermore, there are in particular various exceptions and reliefs if installations are normally operated with gaseous fuels and liquid fuels are only used to a limited extent, e.g. for a limited number of operating hours within defined periods or in the event of an interruption of the gas supply.
This should be checked in particular for plants with multi-fuel burners [especially after the start of the Ukraine war, many plants were (re)equipped with them to counter concerns about a gas shortage]. Often, permission must be obtained from the authorities!
How likely is it that your existing plant will be affected by the new limit values?
In the following section, we would like to give a rough indication of what NOx emissions are usually achieved with existing combustion technology according to our experience.
We do not take into account modern burner technology (such as Weishaupt® 3LN/4LN, Dreizler® ARZ etc.), as this has often been selected with today’s emission requirements in mind and should only be affected in rare cases.
The specified margins refer to the following boundary conditions:
- Worst measured value in the load range
- Burners mounted on Ness thermal oil heaters (large combustion chamber, supply line temperature usually 240 – 280 °C)
- Burners in good maintenance condition and well adjusted
The colouring of the numerical value indicates how high, in our estimation, the need for action is for assumed limit values of 150 mg/Nm³ (natural gas operation) and 200 mg/Nm³ (oil operation) for existing plants:
- Green: Probably no need for action, please check anyway.
- Orange: Action may be required, but please check carefully.
- Red: There is a high degree of certainty that action is required!
Please note that the above information is not binding and that stricter limit values may apply to existing installations, especially in your country. It is essential to deal with this issue!
What else needs to be considered besides exhaust emissions?
(Thermal) Efficiency is a much more important issue than in the past, given today’s energy prices and the desire for more sustainability.
In the past, efficiency-enhancing measures were sometimes foregone, depending on the size of the system, the installation location and the buyer’s budget. In the meantime, however, the issue has come very much into focus, even for smaller installations and in countries with traditionally low energy prices (e.g. USA), and in the majority of cases our customers find that considerable savings can be achieved with relatively small additional investments.
In addition, it is important to note that there may also be regulatory requirements regarding efficiency! In Germany, this is again the 44th BImSchV, which generally specifies a maximum flue gas loss of 9%. In other words, the thermal efficiency must then be at least 91%! At the usual operating temperatures of most thermal oil heaters, this cannot be achieved without additional measures.
How can the thermal efficiency be increased in practice?
A proven method which is independent of external heat sinks is the preheating of combustion air by means of a so-called combustion air pre-heater (German abbreviation Luvo). Here, thermal power from the flue gases, which would otherwise escape unused through the chimney, is used to preheat the intake air of the burner. The resulting fuel saving is reflected in a considerable increase in thermal efficiency (typically by about 6 percentage points).
Despite an increased power requirement for the combustion air fan, very short payback times can be achieved. This can be estimated using our payback calculator, which can be found on the following website: https://www.ness.de/en/heat-recovery/
Based on the table above, it is clear that combustion air preheating tends to increase NOx emissions! Is it then an option worth considering at all?
The answer to this is clearly YES, because this only applies to a comparable technology level! When converting to state-of-the-art low NOx burners, nitrogen oxide emissions can often be significantly reduced – despite retrofitting a Luvo! In many cases this even applies without having to resort to measures such as external exhaust gas recirculation, which would complicate the conversion.
NESS is the right partner for this, because we know the available and already field-tested burner technology in detail!
And what alternative or additional measures are possible?
- If an (external) – ideally also year-round – heat sink is available, this can also be taken into account. This is, for example, the introduction of the hot flue gases into a dryer (depending on the product to be dried and the fuel) as well as the extraction of heat in the form of hot or warm water by means of a heat exchanger. Depending on the respective temperature levels and required heat outputs, these measures can even be foreseen in addition to combustion air preheating!
- Retrofitting an O2 control system to limit the residual oxygen content in the flue gas. It reduces the excess air at the burner and thus reduces the amount of hot flue gas that is discharged via the chimney while the boiler output remains the same. Typically, this increases the thermal efficiency by about one percentage point, and also compensates well for slight fluctuations in the fuel composition.
- Retrofitting a VFD for the combustion air fan to minimise its electrical energy demand. This measure is particularly effective when heaters run at partial load for longer periods. Then the sound level of the fan is also reduced.
Ideally, the selected measures should be carried out simultaneously in order to make the engineering and conversion (mechanical and electrical) as efficient as possible.
Such a conversion is also often a good opportunity to replace obsolete plant controls (replacement of contactor controls with hardware controllers by failsafe PLCs).
NESS is your ideal partner for all these issues. Do not hesitate to contact us!