FAQ – Monitoring of pumps in thermal oil systems
What do I monitor on my pumps in the system and how to proceed best?
In this FAQ area, you will find some general questions and answers on and around the topic of monitoring of pumps in thermal oil system, why this is necessary, and how you can protect your thermal oil system with this.
Why is pump monitoring reasonable in a thermal oil system?
Pumps are the determining components in heat transfer systems with liquid heat transfer mediums.
As „heart“ of the system, they ensure that the heat transfer medium circulates in the system and the thermal energy provided by the heater is conveyed to the right position in the system.
These pumps can be equipped with relatively simple monitoring sensors that bear no relation to the purchasing costs of a new pump. Even a damage on a component of a pump, e.g. a damaged bearing, can be repaired if detected early; otherwise at a later stage, most pumps must completely be replaced. The economic loss because of an unwanted standstill due to damage to the pump or even a fire caused by a leaking pump, more than ever exceeds the costs for a reliable pump monitoring.
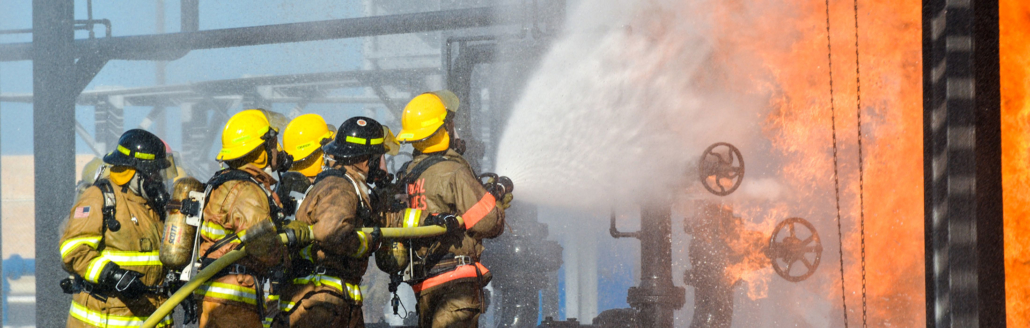
Back to Index
When is pump monitoring reasonable?
Monitoring is always reasonable. Pump monitoring is an important factor in the field of system safety, and it is very easy to implement, also as a retrofitting kit.
Because of the reduced risk, this safety device pays off already from the first day of purchase.
Redundantly designed pump stations provide operating safety in case the main pump fails. However, in case of fire or explosion on the pump station, the redundant pump can be damaged directly or indirectly, and redundancy will not be provided anymore. As a direct damage, for instance, a damage of the cabling can be seen, which is often led over the same cable duct together with the main pump.
Finally, in the sense of operating safety, pump monitoring should always be used.
Back to Index
Which criterions should be considered for monitoring of the pumps?
Beside the standardised inspection of the pump, there are three parameters that should permanently be checked during the operation of the pumps. These parameters include bearing temperature, pump vibration, and leakages of the pump. These should absolutely be part of the monitoring program.
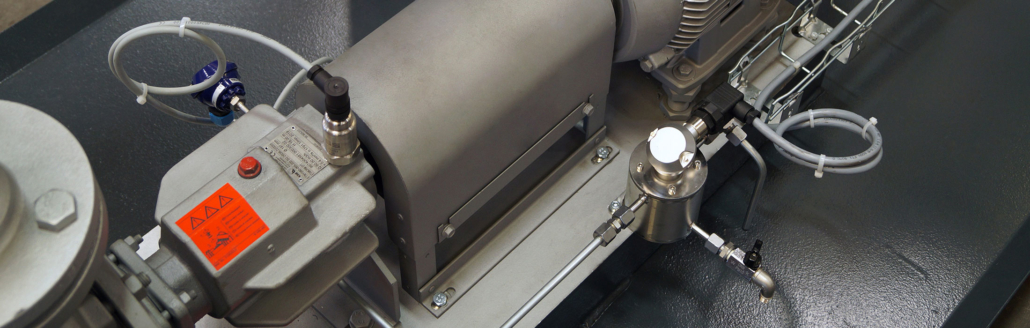
Back to Index
How is pump monitoring integrated in the system?
The necessary sensor circuits are mounted on the pumps and integrated in the already existing system control. The limit values for alarms and switching off are then to be set in the control system depending on the operating environment and the pump used.
Back to Index
Other FAQ topics that might interest you
NESS Pump Monitoring (NPCL/NPCV/NPCT)
Pump monitoring in thermal oil systems